اصطلاح
فولاد یاپولاد برای آلیاژهای آهن که بین ۰/۰۲۵ تا حدود ۲ درصد کربن دارند
بکار میرود فولادهای آلیاژی غالبا با فلزهای دیگری نیز همراهند. خواص
فولاد به درصد کربن موجود در آن، عملیات حرارتی انجام شده بر روی آن و
فلزهای آلیاژ دهنده موجود در آن بستگی دارد.
کاربرد انواع مختلف فولاد
از
فولادی که تا ۰٫۲ درصد کربن دارد، برای ساختن سیم، لوله و ورق فولاد
استفاده میشود. فولاد متوسط ۰٫۲ تا ۰٫۶ درصد کربن دارد و آن را برای ساختن
ریل، دیگ بخار و قطعات ساختمانی بکار میبرند. فولادی که ۰٫۶ تا ۱٫۵ درصد
کربن دارد، سخت است و از آن برای ساختن ابزارآلات، فنر و کارد و چنگال
استفاده میشود. فولاد، انواع فراوانی دارد. که همه آن موارد در جدول کلید
فولاد قابل دسترس می باشد.
ناخالصیهای آهن و تولید فولاد
آهنی که از
کوره بلند خارج میشود، چدن نامیده میشود که دارای مقادیری کربن، گوگرد،
فسفر، سیلیسیم، منگنز و ناخالصیهای دیگر است. در تولید فولاد دو هدف دنبال
میشود:
سوزاندن ناخالصیهای چدن
افزودن مقادیر معین از مواد آلیاژ دهنده به آهن
منگنز،
فسفر و سیلیسیم در چدن مذاب توسط هوا یا اکسیژن به اکسید تبدیل میشوند و
با کمک ذوب مناسبی ترکیب شده، به صورت سرباره خارج میشوند. گوگرد به صورت
سولفید وارد سرباره میشود و کربن هم میسوزد و مونوکسید کربن (CO) یا
دیاکسید کربن (CO۲) در میآید. چنانچه ناخالصی اصلی منگنز باشد، یک کمک
ذوب اسیدی که معمولاً دیاکسید سیلسیم (SiO۲) است، بکار میبرند:
MnO + SiO۲ ----> MnSiO۳
و
چنانچه ناخالصی اصلی سیلسیم یا فسفر باشد (و معمولاً چنین است)، یک کمک
ذوب بازی که معمولاً اکسید منیزیم (MgO) یا اکسید کلسیم (CaO) است، اضافه
میکنند:
MgO + SiO۲ ----> MgSiO۲
۶MgO + P۴O۱۰ ----> ۲Mg۳(PO۴)۲
کوره تولید فولاد و جدا کردن ناخالصیها
معمولاً
جداره داخلی کورهای را که برای تولید فولاد بکار میرود، توسط آجرهایی که
از ماده کمک ذوب ساخته شدهاند، میپوشانند. این پوششی مقداری از
اکسیدهایی را که باید خارج شوند، به خود جذب میکند. برای جدا کردن
ناخالصیها، معمولاً از روش کوره باز استفاده میکنند. این کوره یک ظرف
بشقاب مانند دارد که در آن ۱۰۰ تا ۲۰۰ تن آهن مذاب جای میگیرد.
بالای
این ظرف، یک سقف مقعر قرار دارد که گرما را روی سطح فلز مذاب منعکس میکند.
جریان شدیدی از اکسیژن را از روی فلز مذاب عبور میدهند تا ناخالصیهای
موجود در آن بسوزند. در این روش ناخالصیها در اثر انتقال گرما در مایع و
عمل پخش به سطح مایع میآیند و عمل تصفیه چند ساعت طول میکشد، البته
مقداری از آهن، اکسید میشود که آن را جمعآوری کرده، به کوره بلند باز
میگردانند.
روش دیگر جدا کردن ناخالصیها از آهن
در روش دیگری که از
همین اصول شیمیایی برای جدا کردن ناخالصیها از آهن استفاده میشود، آهن
مذاب را همراه آهن قراضه وماده کمک ذوب در کورهای بشکه مانند که گنجایش
۳۰۰ تن بار را دارد، میریزند. جریان شدیدی از اکسیژن خالص را با سرعت
مافوق صوت بر سطح فلز مذاب هدایت میکنند و با کج کردن و چرخاندن بشکه،
همواره سطح تازهای از فلز مذاب را در معرض اکسیژن قرار میدهند.
اکسایش
ناخالصیها بسیار سریع صورت میگیرد و وقتی محصولات گازی مانند CO۲ رها
میشوند، توده مذاب را به هم میزنند، بطوری که آهن ته ظرف، رو میآید.
دمای توده مذاب، بی آنکه از گرمای خارجی استفاده شود، تقریباً به دمای جوش
آهن میرسد و در چنین دمایی، واکنشها فوقالعاده سریع بوده، تمامی این
فرایند، در مدت یک ساعت یا کمتر کامل میشود و معمولاً محصولی یکنواخت و
دارای کیفیت خوب بدست میآید.
تبدیل آهن به فولاد آلیاژی
آهن مذاب
تصفیه شده را با افزودن مقدار معین کربن و فلزهای آلیاژ دهنده مثل وانادیم،
کروم، تیتانیم، منگنز و نیکل به فولاد تبدیل میکنند. فولادهای ویژه ممکن
است مولیبدن، تنگستن یا فلزهای دیگر داشته باشند. این نوع فولادها برای
مصارف خاصی مورد استفاده قرار میگیرند. در دمای زیاد، آهن و کربن با
یکدیگر متحد شده، کاربید آهن (Fe۳C) به نام «'سمنتیت» تشکیل میدهند. این
واکنش، برگشتپذیر و گرماگیر است:
Fe۳C <---- گرما + ۳Fe + C
هرگاه
فولادی که دارای سمنتیت است، به کندی سرد شود، تعادل فوق به سمت تشکیل آهن
و کربن، جابجا شده، کربن به صورت پولکهای گرافیت جدا میشود. این مکانیزم
در چدنها که درصد کربن در آنها بیشتر است، اهمیت بیشتری دارد. برعکس، اگر
فولاد به سرعت سرد شود، کربن عمدتاً به شکل سمنتیت باقی میماند. تجزیه
سمنتیت در دمای معمولی به اندازهای کند است که عملاً انجام نمیگیرد.
وباسرد کردن سمنتیت فولاد را به وجود می آورند.
فولاد تریپ (به
انگلیسی: TRIP steel) یا فولاد با پلاستیسیته حاصل از استحاله (به
انگلیسی: TRansformation Induced Plasticity Steel) نوعی فولاد است که در
آن از خواص حاصل از استحاله مارتنزیتی در طی تغییر شکل پلاستیک استفاده
میشود. این فولادها به کمک عناصر محلول پایدارساز، عمدتاً از فاز اوستنیت
تشکیل شدهاند اما در اثر اعمال تنش فاز مارتنزیت در آنها ایجاد
میشود.زیرساختار فولادهای تجاری تریپ شامل فریت، بینیت و اوستنیت است.
پدیده
تریپ برای اولین بار توسط زکای و همکاران ایشان در سال ۱۹۶۷ در فولادهای
تمام اوستنیتی با درصد نیکل و کروم بالا مشاهده شد.ماتسومورا و همکاران
ایشان در سال ۱۹۸۷ این پدیده را در فولادهای دارای درصد اوستنیت کم با
۵۰-۶۰٪ فریت آلوتریومورفیک کشف کردند. این فولادها TRIP-assisted Steel
نامیده میشوند.
خواص مکانیکی
تغییرات ازدیاد طول (کرنش) یکنواخت و ازدیاد طول کل فولاد تریپ Fe–15Mn–3Al–3Si wt% به عنوان تابعی از دما؛ نرخ کرنش ε=10-4.s-1
تغییرات استحکام کششی و استحکام تسلیم ۰٫۲% فولاد تریپ Fe–15Mn–3Al–3Si wt% به عنوان تابعی از دما؛ نرخ کرنش ε=10-4.s-1
خواص
مکانیکی فولادهای تریپ به عوامل متعددی از جمله ترکیب، دما، عملیات حرارتی
و مکانیکی انجامشده بر روی قطعات بستگی دارد.پدیدهٔ تریپ باعث میشود که
چکشخواری این فولادها توسط استحالهٔ مارتنزیتی افزایش یافته و گردنیشدن
به تاخیر بیفتد. چندفازی بودن ریزساختار فولادهای تریپ نیز در بهبود خواص
مکانیکی آنها بسیار موثر است.
تاریخ فولاد
ایرانیان قدیم برای
آهن ورزیده و فولاد آبپذیر کلمات جداگانهای داشتند. آهن ورزیده را آهن و
فولاد آبپذیر را در زبان کهن ایران پولاد مینامیدند. در گورستان تپه سیلک
که محققاً میتوان آن را متعلق به ۱۲۰۰ تا ۱۰۰۰ پیش از مسیح دانست، اشیای
باستانی باارزشی کشف شدهاست. یکی از آنها شمشیری است که دست و قبضهٔ آن از
مفرغ ساخته شده و یک تیغهٔ فولادی نازک، روی مفرغ، پرچ شدهاست. همچنین در
این گورستان چنگکهای فولادینی یافت شده که با استادی تمام چکش کاری
شدهاست.
یکی از فلزکاران روسیه شمشیرهای اصیل کهن ایرانی را با روش عکسبرداری میکروسکوپی تجزیه کرد و به این نتایج رسید که:
1- آنچه که در قرون وسطی با نام فولاد موجدار در اروپا رایج شد، در روسیه به نام ایرانی آن بولات یا پولاد معروف بود.
2- این نوع فولاد موج دار دارای سطح آبگونهای شکیلی است که با بیشتر فولادهای ورقهای مواج فرق دارد.
3-
روس ها معتقدند که فولاد موج دار در هند اختراع شد و بعد به ایران آمد.
اما این تحقیقات تفاوت ساخت فولاد ایرانی و فولاد هندی را مشخص میکند.
در
سدهٔ سوم میلادی از گاهنامه کوکویائو چنین بر میآید که چین در زمان
ساسانیان، فولاد را از ایران وارد میکرد. این کتاب به ویژه از خطوط
مارپیچی که در رویهٔ فولاد ایرانی بود سخن میگوید از اینرو باید گفت که
آهنی که از ایران وارد چین میشد، موجدار بودهاست. این امر شک جوزف
نیدهام محقق صنعت آهن و فولاد در چین را تبدیل به یقین کرد که فن موجدار
کردن اگر از ووتز هند نباشد، از ایران پدید آمدهاست.
فولاد پارتی یا
ایرانی که رومیها اغلب از آن سخن گفتهاند پس از فولاد هند در دنیا اول
بود. و امروز بر این باورند که این فولاد از راه قالگذاری صفحههای صاف آهن
ورزیده با گرد زغالچوب در بوتهها ساخته میشد. این روش تولید بعدها به
عربستان، بینالنهرین و دمشق و بالاخره به شهر تولدو در اسپانیا که مرکز
دانش و فنون اسلامی بود، نیز سرایت نمود.
محصولات نیمه ساخته فولاد
شمش
شمش
(به انگلیسی: Ingot) به قالبهای کوچکتر فلزات گفته میشود که برای طلا و
مس و آلومینیوم و نمونههای آزمایشگاهی کاربرد زیادی دارد.
یک شمش آلومینیوم
شمشال
شِمشال
(به انگلیسی: Billet) از فرآوردههای میانی نورد فولاد است که سطح مقطع
آن کوچکتر از ۲۲۵ سانتیمتر مربع است.به فرآوردههایی با سطح مقطع بزرگ تر
از ۲۲۵ س.م. شمش گفته میشود.
چند شاخه شمشال فولاد
شمشه
شمشه (به انگلیسی: Bloom) به شمشال خیلی شبیه است با این تفاوت که سطح مقطع آن بزرگتر از ۲۳۰ سانتیمتر مربع است.
تختال
تَختال
(به انگلیسی: Slab) قطعهای مکعب مستطیل از فولاد معمولاً به ضخامت ۲۳۰
میلیمتر و عرض ۱٫۲۵ متر و طول ۱۲ متر است. تختال یکی از محصولات میانی برخی
کارخانههای فولادسازی است که از آن برای تولید فولاد ورق استفاده میشود.
ریخته گری فولاد
فولاد
مستحکم است با محدوده استحکام کششی از 60000تا حدود 280000PSI. فولاد
همچنین انعطاف دارد و ترکیبی از استحکام و انعطاف پذیری علاوه بر این فولاد
استحکام شکست بالایی دارد و مقاوم به شک است. خواص فولاد کنترل میشود به
وسیله کنترل محدوده آن به وسیله ترکیب آن، مخصوص درصد کربن آن.
فولاد
آلیاژی از آهن و کربن است، که خواص قابل توجهی مانند قابلیت کنترل
مجموعهای از خواص با درصد کربن، برای مثال وقتی کربن وجود ندارد، آهن
کاملاً نرم و ضعیف است. اگر کربن اضافه شود کمتر از 2/0 تا 3/0 درصد،
استحکام افزایشی محسوسی دارد .این اثر کربن روی استحکام کششی و درصد کاهشی
سطح مقطع در فولاد ریختگی کربنی ساده.
منحنیهایی برای استحکام نهایی و درصد ازدیاد طول نشان میدهد که در یک جهتاند. توجه به این مفهوم که کنترل خواص، فولاد بیشتر مورد توجه به وسیله کنترل دیگر خواص، برای مثال عملیات حرارتی.اما به طورخلاصه آهن و فولاد متحمل یک تغییر در ساختار شبکه کریستالی میشود.
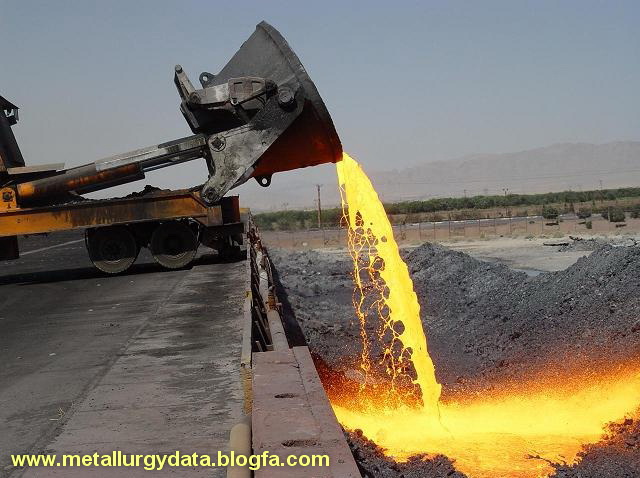
یک نشانه خاص از ریختهگری فولاد در مقایسه با تولید این واقعیت است که قطعات فولادی دارند یک یکنواختی خواص بدون توجه به جهتی که آنها را آزمایش میشود. که این رفتار ایزوتروپیک گفته میشود. این رفتار در فولادی که روی آن کار شده با کار مکانیکی، شکل ساختاری از شمشی یا بیلت زیرا انجام کار خواص جهت داری را نشان میدهد.
بنابراین فولاد کار شده با دوام و مستحکم است وقتی آزمایشی در جهت بزرگترین ازدیاد طول است اما ضعیفتر و شکنندگی بیشتری دارد اگر در جهت عرضی آزمایش شود. فولاد ریختگی این جهتدار بودن را ندارد و از این رو مناسب است برای کاربرد آن زیرا این اثر میتواند اثر مضری را به وجود آورد.
یک فایده خوب قطعات ریختگی فولادی قابلیت جوشکاری آسان آن است که در دیگر آلیاژهای آهنی وجود ندارد. در واقع فولاد میتواند باشد قابل جوشکاری باشد.
شاید پتانسیل مهم این مواد امکان ترکیب آنها است به وسیله قطعات ریختگی فولاد جوش داده شده یا شکلهای ساخته شده به روشهای دیگر، تولید ساختار ترکیبی قسمتی از قطعات ریختگی و قسمتی فولاد کار شد.
خواص آهنی بیشتر، یکی از فواید وسیع فولاد است، برای مثال، استحکام و انعطاف پذیری، که باعث اشکالات معینی در ریختهگریمی شود. بعد از ریختهگری، جدا میشود حجم را و تغذیه موجود در آن زیرا به علت انعطافپذیری و استحکام جدا کردن آن مشکل میشود و فقط چکشکاری برای آلیاژهای تردتر مانند چدن است. اره کردن، برش با چرخ ساینده، مشعل و غیره برای این هدف مورد نیاز است.
ترکیب خوبی از خواص ریخته گری در فولاد قبل از این گفته شد.از نقطه نظر روش ریختهگری، هر چند، سختگیری برای آمادگی طراح و متالورژیست به علت خواص ریختگی و محدوده بسته از ترکیبات است. ریختن فولاد در درجه حرارت بالا همچنین در خواستها برای توجه ویژه به سوژههای مورد نیاز، پاتیلها، ماسههای قالبگیری، تبدیل فلز به شکل پر کردن قالب و بدون نیامد، و گزارش مسئله. انقباض انجماد بالای فولاد همچنین معرفی طرح و مسائل قالبگیری به ندرت بیشتر از دیگر فلزات میشود. در ذوب این آلیاژها مسایل ویژه زیاد یا بیمانند در فولاد.
طبیعت آلیاژها و واکنشپذیری آنها با اکسیژن و ناخالصیهای آنها، نیازمند روش پیچیده برای ذوب کردن و تصفیه برای ساخت استفاده شود برای اطمینان از تولید خوب و با کیفیت فلز است.
فرآیندهای قالبگیری و ماسهها
قالبگیری برای قطعات ریختگی فولاد تفاوتی با دیگر آلیاژها ندارد. هر چند به علت مشخصات معلوم در فولاد، مطمئناً این روشها نمیتوان استفاده از روشهایی که به طور وسیع در دیگر فلزات استفاده میشود. فولاد میتواند ریخته شود به درون هر قالب ساخته شده با وسیله فرآیندهای قالبگیری ماسهای.
قالبهای ماسه خشک، قالبهای ماسه ماهیچهها، قالبهای پوستهای خشک شده و قالبهای با چسب سیمانی استفاده میشوند در سمت بالایی در ریختهگری فولاد که بیش از ریختهگری سایر آلیاژهاست. دلیل این شرایط سخت به وسیله اثر فولاد است.
با مراجعه به روشهای قالبگیری از دیگر ماسه استفاده میشود. به دلیل درجه حرارت بالای ریختن فولاد از ریختهگری در قالب دائمی خودداری میشود، مگر در حالتهای خاص، یا به وسیله قالبهای دای کست، یا قالبهای گچی.
فولاد میتواند ریختهگری شود در قالبهای دقیق زیرا مواد قالبگیری دقیق به اندازه کافی شور است. قالبهای گرافیتی میتواند استفاده شود برای فولاد اگر پیشبینی شود در جلوگیری از گرفتن کربن قالبهای سرامیکی نیز همچنین استفاده میشوند.
قالبگیری با ماسه تر
تعدادی قطعات فولادی ساخته میشوند با استفاده از قالبهای ماسهتر. روشی عمومی آن از دیگر فلزات متفاوت نیستند. هر چند ماسههای ریختهگری فولاد متفاوت از دیگر که مخصوصاً وابسته به مشخصات آن است.
دیرگدازی
جهت اینکه ماسه در تماس با فولاد ممکن است گرم شود تا درجه حرارتهای بیش از اندازه، ماسه قالبگیری باید باشد به اندازه کافی خالص زیرا ذوب نشود و خراب نشود قالب.این ماسه در یک سطح مشترک فلز ـ قالب که ممکن است به درجه حرارت بالا برسد یک نتیجه از نیاز برای پایداری حرارتی بالا، در بیشتر ماسه قالبگیری تر وجود دارد با ترکیبات مخلوطهایی از ماسه که چسب معمولاً بنترنیت است.
در رابطه با شور بودن ماسه که مقاومت و پایداری آن مسئله مهمی است. در درجه حرارت بالا ماسه یک تغییر حالت از خود نشان میدهد و هر دو پیوند فیزیکی و شیمیایی، به طور تدریجی خواص آن تغییر میکند. مگر اینکه به مقدار زیاد ماسه جدید دوباره اضافه شود.
متأسفانه روش آزمایشی که نشان دهد این تغییر حالت تدریجی را وجود ندارد.در یک بررسی در مشاهده این سرعت خراب شدن ماسه مرتبط است با افزایش نسبتاً بالای استحکام گرم و حساسیت در برابر شوک حرارتی با توسعه سافت پوششهایی روی دانههای ماسه است.
نفوذپذیری بالا و درصد رطوبت کم
این دو خواسته مرتبط به یکدیگرند زیرا به هم وابسته هستند. وقتی ماسه گرم است، قسمتی از رطوبت در ماسه تبدیل به بخار میشود. هوا در قالب گرم میشود و حجم آن افزایش مییابد و ترکیبات موجود در آن ممکن است تجزیه شود به مواد گازی. مقداری از این گازها خارج میشود از حفرات قالب.
گرمای فولاد در قالب بیش از درجه حرارت دیگر فلزات است، از این رو حجم گاز بیشتری ممکن است تولید شود و نیاز به خارج شدن بیشتری است. شرایط لازم میتواند برای رسیدن فولاد میتواند باشد به وسیله افزایش نفوذ پذیری در حدود مورد نیاز برای دیگر آلیاژها و محدودیت درصد رطوبت که نسبتاً حجم کمی است (حدود 3درصد). بیشتر گاز فرار کند از تغذیهها و دیگر حفرات در قالب.
ترکیبات عالی و غیره
استفاده از ترکیب ماسهها با نسبتاً درصد کم چسب برای فولاد که همراه است به وسیله تمایل به سوی عیبهایی مشخص در قطعات مانند پوسته پوسته شدن، باد کردگی و رگهای شدن آن از نتایج از انبساط ماسه در اثر حرارت است. اضافه کردن مواد مشخصی ممکن است کاهش دهد .
اثر اساسی از این شرایط خاص که تحمیل میشود به فولاد به وسیله نتیجه خواص ماسه تر در ساخت در محدودهای که خواص آن به طور مشخصی متفاوت از مخلوط ماسه قالبگیری برای دیگر آلیاژها است. این تفاوتها نشان داده شدهاند به وسیله اطلاعات جدول9-5 که ترکیب و خواص از ماسه برای آلیاژهای مختلف و فولاد که شامل آنها میشود لیست شده است بیشتر ماسه تر استفاده میشود با ماسه رویی که مخصوصاً ترکیب تولید شده این خواص را خواهد داشت (برای ماسه رویی) و ماسه چشت بند که اساساً استفاده مجدد از ماسه رویی است، که همچنان اندازه دانه آن وخواص آن کنترل میشود. این روش، اگرچه پیچیدگی بیشتری دارد وقتی قالبگیری با هر دو ماسه پشت بند و ماسه رویی برای قالبگیری است.
عیوب قالبگیری با ماسه تر
علاوه بر عیوبی مانند، پوسته پوسته شدن، بادکردگی و رگهای شدن، پارگی گرم و غیره که در جای دیگری از کتاب توضیح داده شده، و همچنین ترکهای سرتاسری در مراجعه به دیگر مواد، عیب دیگری که میتواند افزایش یابد سوراخ سنجاقی است. که مشخصاً آن حفرات کوچک در دیواره صاف است، که باریک در یک جهات ستونی به سمتدیوار، قالب که بلافاصله قبل از پوسته قطعه ریختگی به وجود میآید.
علت به وجود آمدن این عیب هنوز جای بحث دارد، اما خواص عمومی در تشکیل هر یک از CO یا H2O یا هر دو به وسیله یک واکنش در سطح فلز این واقعیت که عیوب رخ میدهد به طورمکرر در قالبهای ماسه تر به این موضوع اشاره دارد که در اضافه کردن کم به وسیله شرایط مشخص وجود دارد در سطح مشترک ماسه و فلز، و وقتی تنها تفاوت بزرگ بین ماسه تر و قالبهای ماسه خشک باید درصد رطوبت آن باشد.
تشکیل H2O یا هر دو به وسیله واکنش بین هیدروژن و اکسیژن در فولاد باید به حداقل فاکتور توزیع را داشته باشد. رطوبت در ماسه، شرایط را بدتر میکند به وسیله شرکت هیدروژن وقتی نفوذ میکند به داخل فولاد و واکنش میکند با اکسیژن حل شده. این توضیح میدهد که چرا با اکسیژن زدایی فولاد توسط آلومینیوم قبل از ریختن حفرات متخلخل کاهش مییابد وقتی اکسیژن واکنش میدهد با آلومینیوم به جای هیدروژن.
قالبهای ماسه خشک و قالبهای پوسته ای خشک شده
قالبگیری با ماسه تر ترجیح داده میشود به دیگر روشهای قالبگیری زیرا از نظر اقتصادی بهتر است و سرعت تولید نیز بالاتر است. اما به علت افزایش استحکام قالب یا جلوگیری از حفرات یا برای دلایل دیگر، خشک کردن قالب قبل از ریختن مناسب است. خشک کردن سطحی میتواند انجام شود به وسیله گرم کردن سطح با شعله، لامپ مادون قرمز، هوای داغ، یا قالبهایی که میتوان خشک کرد در یک نوع کوره ماشین بزرگ در درجه حرارت بالای °F500.
درصد رطوبت در ماسه تر استفاده شده برای قالبهای خشک شده سطحی یا قالبهای ماسه خشک ممکن است مقداری بالاتر از ماسه تر معمولی برای قابلیت قالبگیری بیشتر، و همچنین با علت رطوبت بالاتر هدایت میکند به سمت استحکام خشک بالاتر.
انواع دیگر قالبها
تعدادی از ریختهگران از سیمان به عنوان چسب ماسه استفاده میکنند، اما این روش خیلی در این کشور معمول نیست.
ریختهگری دقیق برای قطعات ریختگی ویژه که تلرانس دارند و یا پیچیدگی در طراحی استفاده از این روش انجام میشود. یکی از زمینههای قالبگیری دقیق که مؤثر است در ریخته گری آلیاژهای ویژه و شکلهای استفاده شده برای پرههای توربین گاز و دیگر قسمتهایی که موضوع آن کار در درجه حرارت بالا نمیتوان شکل داد به خوبی به وسیله دیگر روشها.
قالبهای پوستهای تا مقداری با موفقیت استفاده میشوند اما گرایشی به عیوب سطحی در آن وجود دارد.
این اینها را میتوان حذف کرد به وسیله استفاده از نوعی مبرد در قالبهای پوستهای. قالبهای سرامیکی نیز همچنین امکانپذیر است. که ریختن قسمتهای نازکتر از قالبهای ماسهای که مرسوم است را اجازه میدهد. فرآیند مخصوص ترکیب قالبهای گرافیتی و ریختن با فشار هوا استفاده میشود برای توید چرخهای فولادی ماشین و دیگر قطعات.
روشهای قالبگیری
روشهای معمول در قالبگیری ماند کوبش دستی، کوبش ضربه ای، فشردن و روش کوبش و پرتاب ماسه، که در ماسههای فولاد استفاده میشود. و هیچ تفاوتی وجود ندارد بین روشها استفاده شده برای فولاد در مقایسه با دیگر آلیاژهای ریختگی.
ماهیچهها
علاوه بر نیاز به تهیه مخلوط ماسه ماهیچه برای بکار بردن در درجه حرارتهای بالاتر، یک تفاوت اساسی وجود دارد بین ماهیچه برای فولاد در مقایسه با ماهیچهای که در دیگر فلزات به کار برده میشود، و اصول آن در بخشهای گفته شده در بالا قابل خواندن است برای ریختهگری فولاد.
به علت شرایط زیاد در افزایش درجه حرارت ریختن استفاده شده برای فولاد، مشکلات ویژه مشخصی باید ذکر شود. یک اثر برای مثال در درجه حرارت ریختن بالا ماهیچه سریعتر گرم میشود و درجه حرارت بالاتر از ماهیچهها برای قطعات ریختگی مشابه در آلیاژهای با نقطه ذوب پایین است. نتیجه این است که حجم بیشتری از گاز ماهیچهها تولید میشود و بیشتر وارد قالب میشود. که این باعث اجبار در قابلیت نفوذ پذیری بالاتر برای قطعات ریختگی فولادی نیاز است که در بیشتر چدنها و قطعات غیر آهنی کمتر است. اطلاعات نشان میدهد که نفوذپذیری بیشتری در ماسههای استفاده شده برای ماهیچههای فولاد وجود دارد. استفاده از جعبه ماهیچه پوستهای کمک قابل ملاحظهای به حذف مشکل گاز تولید شده توسط گاز میانجامد.
دیگر عیوب مرتبط با ماهیچهها در ریختهگری فولاد در پاراگرافهای زیر توضیح داده شده است.
پارگی گرم
فولاد در درجه حرارت بالا ریختهگری میشود. اما این درجه حرارت نسبتاً کم است به دلیل محدوده درجه حرارت کوتاه انجماد در فولاد. نتیجه این که این فولاد خیلی زود بعد از ریخته شدن شروع به انجماد میکند. و در بعضی موارد قبل از گرم شدن ماهیچهها که آنها استحکام خود را دارند. ترکیبی از استحکام نسبی ماهیچه و انقباض ضعیف فلز اغلب باعث تغییر شکل شکست در قطعات ریختگی که اشاره به ترک گرم دارد.
فولاد تنها فلزی نیست که موضوع ترک گرم در آن وجود دارد، بلکه این عیب در دیگر فلزات نیز وجود دارد اما این مشکل در ریختهگری فولاد شدیدتر است، و در این فصل علل ترک گرم مطالعه خواهد شد. نمیتوان گفت ماهیچهها تنها علت ترک گرم هستند وقتی که استحکام قالب همچنین علتی اساسی در ترک گرم. وقتی ماهیچهها تولید میشوند اغلب مستحکمتر از قالبها، عیب ترک گرم به نسبت توضیح داده میشود با ماهیچهها.
ترک رخ میدهد وقتی انقباض طبیعی فولاد جلوگیری میشود به وسیله هر یک از شکل هندسی ریختگی یا بوسیله قالب، دیگران مدارکی که نشان میدهد ترک گرم رخ میدهد بعد از انجماد. در این حالت ترکها ممکن است ریز باشد، مرز شکستها، قابل دیدن نیست بدون استفاده از مایعات نفوذپذیر (فلورسنت) و یا اچ کردن مشاهد نمیشود.
