حرارت به سه طریق منتقل می شود : 1- هدایت. 2- جابجائی. 3- تشعشعی
کوره های زمینی اگر چه از قدمت زیادی برخوردار است و تکنولوژی ساخت کوره های جدید آن را تحت الشعاع قرار داده است، اما بایستی توجه داشت که در شرایط خاص استفاده از ان هنوز با اهمیت تلقی می شود. این کوره ها به علت سادگی ساخت ، سهولت شرایط کار ،ارزانی و کیفیت مذاب خوب تا به امروز در کارگاههای کوچک مورد استفاده قرار می گیرد.
اصولا برای طراحی کوره بایستی چند عامل را در نظر گرفت:
1. ارتفاع کوره بایستی در حد اپتیمم باشد.یعنی حدی که بالاترین رانمان حرارتی و اقتصادی را دارا باشد. در تعیین ارتفاع بایستی حداقل ارتفاعی که بالاترین رانمان حرارتی را جهت ریخته گری بوجود آورد در نظر گرفته شود. .از آنجا ییکه قطر کوره های زمینی متفاوت است. و از طرفی ارتفاع کوره با قطر آن رابطه مستقیم دارد، بنابراین رابطه تجربی را می توان در نظر گرفت
استقرار دهانه فارسونگ :
موقعی راندمان ریخته گری در رابطه با فارسونگ بالاترین حد خود را داراست که:
الف: امتداد لوله فارسونگ در ارتفاعی نصب گردد که حد فاصل بین ته بوته ای و بوته باشد.
ب: لوله فارسونگ طوری نصب گردد که امتداد آن حتی المقدور مماس با جداره کوره باشد. در غیر این صورت سوخت با برخورد به دیواره از سرعتش کاسته می شود و بدین ترتیب سوخت مایع که در اثر هوای دم به صورت پودر درآمده با برخورد به دیواره کوره به صورت قطره درآمده و سوخت کامل نخواهد بود
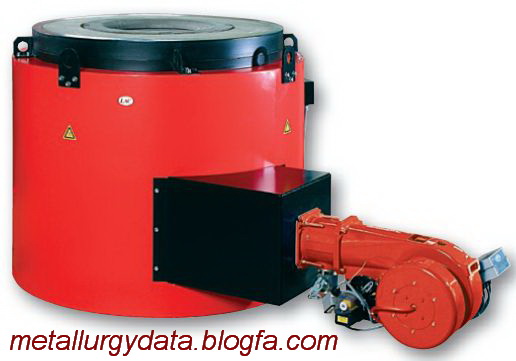
با توجه به شرایط طراحی کوره می توان بدنه خارجی کوره را از ورق آهن به ضخامت 5 تا 10 میلی متر تهیه نمود. ته این بدنه استوانه ای نیز از جنس خودش بوده و بوسیله دریچه ای متحرک بازو بسته می گردد. ضمناً سوراخ کوچکی در یک گوشه دریچه پاین جهت خروج آشغال و شیره های ته کوره تعبیه گردیده است.ضخامت جداره کوره نبایستی از حد معینی(5 میلیمتر) کمتر باشد،زیرا ضخامت کمتر از این مقدار باعث تغییر شکل جداره در اثر گرما گردیده و در نتیجه باعث از هم پاشیدگی کوره خواهد شد.
امروزه نسوز کوره های زمینی را بیشتر آجرهای فرم تشکیل می دهد. نحوه چیدن آجرها از ته کوره تا دهانه آن بایستی با توجه به طراحی کوره انجام گیرد. در ضمن دهانه فارسونگ نیز آجر فرم مخصوص خود را دارد.ته کوره نیز از آجرهای نسوز حدود 3 سانتی متری می پوشانند و روی آن را با خاک نسوز با اندکی شیب به طرف سوراخ خروج آشغال ته کوره اندود می کنند.آجرهای شاموتی معمولاً مناسبترین دیر گداز و اقتصادی ترین آجرها برای ساخت کوره های زمینی می باشد. این آجرها در شرایط مذاب گیری این کوره ها عمر نسبتاً خوبی دارند. آنها دارای مقاومت در برابر شوک حرارتی خوبی بوده و نقطه زینتر بالایی دارند.
3. دم کوره :
4. لوله فارسونگ:
لوله فارسونگ جهت رساندن سوخت به کوره داخل لوله دم نصب گردیده است، بطوریکه هوای دم در حین ورود به کوره سوخت را که بیشتر بصورت مایع است را به صورت پودر مانند کرده و به کوره می رساند تا احتراق به طور کامل انجام شود.
5. بوته های ذوب : ( جنس بوته ها)
بوته های آهن خالص- بوته های فولادی- بوته های چدنی- بو ته های شاموتی- بوته های گرافیتی- بوته های سیلیکون کاربیدی- بوته های دیگر.
آهن خالص برای فلزاتی که نقطه ذوب کمتری نسبت به آهن دارند و خوردگی کمتری دارند- از بوته های آهنی برای ذوب موادی که نقطه ذوب آنها پائین تر از نقطه ذوب آهن خالص است (1539-1536درجه سانتیگراد) استفاده میکنند. منیزیم را در داخل این بوته ذوب می کنند، چون با بهترین آجر نسوز نمی توان منیزیم را ذوب کرد و دلیل آن نیز میل ترکیبی منیزیم با اکسیژن است که اکسیژن نسوز را جذب می کند و نسوز متخلخل می شود.
آهن خالص تجاری:
چون آهن بصورت خیلی خالص بندرت یافت می شود , بیشتر از این آهن استفاده می شود و خلوص آن 8/99% است و ناخالصی اش 2/0-1/0% می باشد. آهن خالص تجاری را در دنیا برخی از شرکتها از جمله شرکت آرمکو و وستینگ هاوس در آمریکا تولید می کنند که برای ذوب آلیاژهای با نقطه ذوب کم مثل روی , منیزیم , سرب و ... از این ورقها بوته درست کرده (بوته یکپارچه)و استفاده می کنند (بوته را جوش نمی زنند بلکه آن را با پرس و گرم کاری شکل می دهند.)- از بوته های چدنی برای ذوب آلیاژهای روی , آلومینیوم و سایر آلیاژها با نقطه ذوب پائین استفاده می کنند به شرطی که مشکل آهن در آن آلیاژها وجود نداشته باشد . تجربه نشان می دهد مذاب Al و Zn , آهن را در خود حل می کنند، چون چدن دارای انتقال حرارت خوبی است (بدلیل گرافیتهای لایه ای) و ارزان ریخته گری می شود . در ایران بیشتر از بوته های چدنی استفاده می شود .
از بوته های فولادی برای ذوب آلیاژها با نقطه ذوب کم و آلیاژهائی که میل ترکیبی زیادی نسبت به اکسیژن دارند مثل آلیاژهای منیزیم که علاقه دارند اکسیژن مواد نسوز را جذب کنند , استفاده می کنند . فولادهای معمولی خوردگی بیشتری دارند و مذاب آلیاژهای مختلف تدریجاً آن را می خورند (یعنی بدنه را در خود حل می کنند).
بوته های گرافیتی :
همانطور که از نام این بوته ها پیداست , جنس این بوته ها از گرافیت می باشد . (می دانیم که کربن در طبیعت به سه صورت دیده می شود : 1) کربن بی شکل : این کربن شکل بلوری ندارد و به آن کربن آمورف نیز می گویند . این کربن در اثر حرارت در مجاورت اکسیژن , می سوزد و خاکستر از آن باقی می ماند. 2) کربن بصورت گرافیت : این نوع کربن بصورت بلوری (کریستالی) می باشد و بلوری آن طوری است که دارای صفحات لغزش است و این صفحات می توانند روی هم براحتی بلغزند . بهترین آنها گرافیت چرب نقره ای است . این گرافیت ماده نسوز است و نقطه ذوبی در حدود بیش از 3000 درجه سانتیگراد دارد گرافیت راسب (رسوب یافته) شده در حین انجماد در چدنهای خاکستری از این نوع است که از مذاب جدا شده . 3) کربن بصورت الماس : بلور این نوع کربن بصورت یک هشت وجهی است ولی رنگی و شفاف است و با سختی 10 موهس سخت ترین ماده در طبیعت می باشد .
بوته های سیلیکون کاربید :
بوته های شاموتی :
این بوته ها از خاک رس نسوز ساخته می شود . از ریختن رس نسوز در اثر حرارت اصطلاحاً شاموت به دست می آید . البته درجه نسوز بوته های شاموتی بستگی به درجه خلوص شاموت دارد . بهترین ماده شاموت آنست که پس از پخت , مقدار فازهای مولایت در حداکثر خود قرار گیرد (1800 0C . 3Al2O3 . 2SiO2).
انواع کوره های بوته ای : Crucible Furnaces
الف) کوره بوته ای چرخان:
1- چرخان حول تقریباً کمی بالاتر از مرکز ثقل
2- چرخان حول محور ناودانی کوره
ب) کوره بوته ای ثابت (زمینی) :
1- با سوخت جامد - این نوع کوره ها دو نوعند,یکی کوره سنتی است که از سوخت جامد زغال سنگ یا کک برای عمل ذوب استفاده می کردند.این نوع کوره نیاز به برق نداشت و با هوای طبیعی که از زیر کوره از لابه لای میله های کف به داخل کشیده می شد زغال سنگ یا ککها را مشتعل می ساخت . برای ذوب فلزات مخصوصاً چدن بوته را در داخل ککها دفن می کردند تا هم از بالا و هم از بغل ها و هم از زیر حرارت به فلز برسد و ذوب خوب و کامل انجام شود. (برای ذوب چدن در این کوره ها اول باید ککها را الک کرد یعنی ککها را دسته بندی کرد از درشت به ریز و پودر,کک درشت در زیر و بعد بوته و بعد شارژ و چند کک گنده در داخل بوته و کک متوسط در اطراف و ریزها را در اطراف می ریزیم و بقیه را در بالا می گذاریم.
2- با سوخت مایع –, سوخت این کوره ها از گازوئیل با ارزش حرارتی 9300 کیلو کالری بر لیتر درجه سانتیگراد یا مازوت با ارزش حرارتی 1100 کیلو کالری بر لیتر درجه سانتیگراد است و می توان با استفاده از بوته های گرافیتی در آن چدن ذوب کرد. مشعل آن از نوع فارسونگاهی(یک نوع مشعل ساده صنعتی که از طریق یک لوله رابط به یک ونتیلاتور(دمنده هوا) وصل شده است).نوع ونتیلاتور یا دمنده هوا بستگی به ظرفیت کوره انتخاب می شود , معمولاً دمنده هائی که پس از ساخت بالانس شده اند را در این کوره ها قرار می دهند (در تهران ,مظفریان و در تبریز,کارخانه متحد) بدنه کوره از اسکلت فلزی است , از تکه لوله های 40 اینچی یا بالاتر از آن به ارتفاع 130 سانتیمتر و اگر نبود از ورق 6 mm به بالا رول کرده و به هم جوش می زنیم .قطر داخلی 100 و ارتفاع 130- 110 cm پس 100*14/3=314 cm قطر داخلی بدنه می باشد که از جوش زدن ورق گسترده بدست می آید. و در کف بدنه رول شده رینگ می زنیم و میله های در جای خالی رینگ جوش می دهیم رویش آجر نسوز با کمی شیب قرار می دهیم تا سرباره ها بیرون رود , بعد کف بوته قرار داده می زنیم که کف بوته می تواند بوته شکسته باشد و سپس از پائین به بالا نسوز کاری می کنیم که نسوز جداره 20- 15 cm است. فارسونگاه را طوری می گذاریم که بصورت مماس به کف بوته بخورد تا شعله دور بزند.
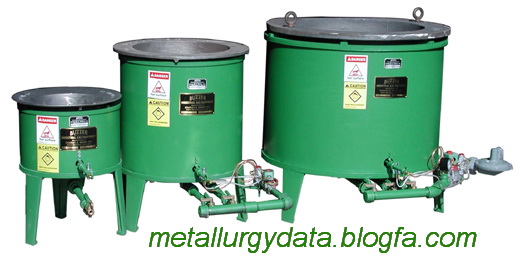