طبق تعریف ماسه عبارت است از ذرات ریز مواد معدنی که قطر آنها از 0.05 تا 1 میلیمتر تغییر می کند.ماسه های مورد استفاده در انواع مختلف با توجه به:
- ترکیب شیمیایی
- درجه دیرگدازی
- نحوه توزیع دانه ها
- در دسترس بودن به کار گرفته می شوند.
انواع ماسه قالب گیری ریخته گری:
ماسه ها انواع مختلفی دارند که از آن جمله میتوان به موارد زیر اشاره کرد:
ماسه سیلیسی:این ماسه به طور گستردهای در ریخته گری به کار میرود و عمدهترین ماسه مصرفی محسوب می شود.ترکیب اصلی آن سیلیس SiO2 است.
ماسه زیرکن:ماسه زیرکن که با فرمول شیمیایی ZrSiO4 مشخص می گردد و به عنوان یک ماسه با نقطه گداز بسیار بالا مورد توجه است.
ماسه کرومیتی:کرومیت یا FeCr2O4ترکیب اصلی این ماسه است و از آن در ریخته گری فلزات با نقطه ذوب بالا استفاده می شود.
ماسه اولوین:ترکیب این ماسه Fe2SiO2 یا Mg2SiO2 است و مخلوطی است از سیلیکات منیزیم و به عنوان ماسه جایگزین در بسیاری نقاط مورد توجه است.
ماسه شاموتی:ماسه شاموتی نوعی کوارتز دانه ریز است که حرارت زیاد دیده است و به عبارت دیگر ماسه ای است که از زینتر کردن ذرات خاک رس به دست می آید.
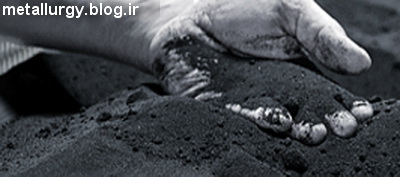
نگرشی به ماسه های سیلیسی مصرفی ایران
ماسه های مصرفی به دو نوع ماسه های با چسب طبیعی و ماسه های مصنوعی تقسیم میگردند.
1) ماسه با چسب طبیعی:
ماسه با چسب طبیعی محتوی تا 20 درصد خاک ریز و مواد ناخالصی می باشد.کیفیت این نوع ماسه برای قالبگیری ماهیچه سازی بستگی به:
- مقدار چسب
- ترکیب شیمیایی ناخالصی
- نوع مذاب ریختگی دارد
این ماده در طبیعت بصورت پیش آماده شده وجود دارد.برای استفاده از این نوع ماسه ها تنها مرطوب کردن آنها کافیست از این نوع ماسه در ریخته گری فلزات غیر آهنی با نقطه ذوب پایین نظیر آلومینیوم،برنج ها،برنز ها و قطعات کوچک چدنی استفاده میشود.بطور قطع اینگونه ماسه ها برای ریخته گری قطعات بزرگ چدنی مناسب نیست معایب عمده این نوع ماسه ها عبارت از:
الف- پایین بودن درجه دیرگدازی
ب- همراه داشتن درصد تقریبا زیادی اکسید های قلیایی و آهک می باشد.
وجود اسیدهای قلیایی در این نوع ماسه باعث پایین آوردن درجه دیرگدازی آن گشته و در نهایت باعث ایجاد عیوبی نظیر ماسه سوزی و چسبیدن ماسه به قطعات ریختگی می شود.از طرف دیگر مواد آهکی در اثر حرارت دیدن به صورت گاز درآمده و در صورتیکه قطعات ریختگی بزرگ و دارای ضخامت زیاد باشند فرصت ورود به مذاب را داشته و در قطعات ریختگی به صورت مک و حفره های گازی باقی می مانند.
از آنجائیکه این ماسه در نقاط مختلف ایران به وفور یافت می شود و نسبتا ارزان در دسترس ریخته گران قرار می گیرد.لذا در اکثر واحدهای کوچک و متوسط ریخته گری ایران به طور وسیعی در مواد قالبگیری و ماهیچه سازی مصرف دارد. ماسه های گرگان ،رشت،گرمسار،اردکان یزد،حسن آباد قم،عین آباد ،محلات و اطراف یزد جزء این گروه ماسه ها هستند.
ماسه های طبیعی بر حسب میزان خاک رس موجود در آنها به سه دسته تقسیم می شوند:
1- ماسه ضعیف که حداکثر تا 8% خاک رس دارد.
2- ماسه متوسط که بین 8 تا 18 % خاک رس دارد.
3- ماسه خاک یا ماسه ملات که بیش از 18% خاک رس دارد.
معمولا خاک ماسه های طبقات زیرین بیشتر از لایه های سطحی می باشد و ریختگران بایستی پس از آزمایشات دقیق،ماسه مطلوب خود را تهیه نمایند.در ریخته گری معمولا از ماسه های متوسط استفاده می شود.
2) ماسه های مصنوعی:
ماسه مصنوعی از شکستن ،خرد کردن و غربال کردن سنگهای سیلیس به دست می آیند که با اضافه کردن چسب و مواد دیگر قابلیت قالبگیری در آنها ایجاد می گردد.
ماسه مصنوعی در مقایسه با ماسه طبیعی دارای مزایای زیر می باشد:
- درجه دیرگدازی و خلوص بالاتر.
- سهولت در کنترل مشخصات فیزیکی و مکانیکی مخلوط.
- قابلیت بازسازی و مصرف مجدد.
- در دسترس بودن.
محدودیت اصلی ماسه های مصنوعی در مقابل ماسه های طبیعی بالا بودن قیمت تمام شده آنها می باشد .با این وجود این ماسه ها می توانند بخوبی نیازهای صنایع ریختگری ایران را در زمینه چدن و فولادریزی(به استثنای فولادهای خاص که به مصرف ماسه های زیرکونی-کرومیتی و اولوینی نیاز دارند) تامین کنند.
ماسه ها ی سیلیس مصنوعی رایج ترین ماسه ها قالب گیری در واحدهای ریختهگری می باشد و انواع ذرات سیلیسی به عنوان ماده اصلی و دیر گداز ماسه ریخته گری به کار می رود .بیشتر ماسه های قالب گیری از کوارتز معدنی که میتواند تا دمای 1700 درجه سانتیگراد را تحمل کند تشکیل شده است.شکلهای دیگر سیلیس تریدیمیت و کریستومالیت میباشد.
وجود اکسید های آلومینیوم و آهن خاصیت دیرگدازی ماسه را افزایش میدهند و حضور اکسید های پتاسیم و سدیم و ترکیبات میکا چسبندگی و شکل پذیری ماسه را زیاد و قابلیت دیرگدازی آن را کاهش می دهد و لذا در ترکیبات ماسه سیلیس وجود اکسید های قلیایی و قلیایی خاکی مضر تشخیص داده میشود. علاوه بر مسئله فوق وجود انواع اکسید ها باعث ایجاد رنگهای قرمز و قهوه ای،اکسید های سدیم و پتاسیم رنگ ماسه را متمایل به آبی می نماید .علاوه بر ترکیبات شیمیایی که خاصیت دیرگدازی ماسه را تحت تاثیر قرار میدهد مشخصات فیزیکی ماسه مانند اندازه ،پخش و شکل ذرات نیز باید مناسب باشد.
نگرشی به ماسه های کرومیتی و اولیونی ایران
کرومیت و اولوین در صنایع ریخته گری دارای مصارف متعدد و متنوع بوده و لذا ضرورت شناخت منابع آن در ایران و جایگزینی مواد بومی به جای منابع وارداتی وجود دارد.
موارد اصلی مصرف کرومیت و اولیوین در صنایع ریخته گری به قرار زیر است:
1- در ساخت جداره کوره ها-پاتیل ها و ابزارهای کمکی ذوب و استفاده از آنها به عنوان یک دیرگداز مناسب از منابع داخلی.
2- به عنوان یک ماسه مناسب ریخته گری در تولید.
3- انواع فولادهای ریختگی بویژه فولادهای استنیتی منگنزی.
4- قطعات بزرگ چدنی.
5- استفاده از آنها به عنوان ماسه رویه در تولید سری قطعات چدنی(قالبگیری ماشینی و استفاده از ماسه تر) بویژه در قسمتهای فوقانی قطعات که تمایل به ماسه ریزی(ناشی از انبساط غیر پیوسته ماسه سیلیسی) دارند.
پودر کرومیت و اولیوین را می توان در تهیه بعضی از دوغاب های اولیه دیرگداز در ریخته گری دقیق استفاده کرد و ماسه های کرومیتی و اولوینی نیز می توانند به عنوان دیرگداز در پشت بند(بویژه در مورد قالبهای سرامیکی) مورد استفاده قرار گیرند.
بررسی ماسه های قالبگیری و ماسه ماهیچه در فرآیند ریخته گری قالب موقت
ماسه ی قالبگیری:
سیلیس (sio2 )، مهمترین جزء ماسه های مصرفی در قالبگیری می باشد، این ماده دارای دیر گدازی بالامیباشد و می توان از ماسه های طبیعی که معمولا دارای اندازه ای یکنواخت و کروی هستند این ماده را بدست آورد و یا با عمل شکست در ماسه سنگ های بزرگ ، ماسه ای با ذرات زاویه دار و اندازه غیر متناسب تهیه نمود. در ماسه ها ی قالبگیری خواص فیزیکی بسیار مهم است . معمولا ماسه ها بصورت کروی و دانه بندی یکنواخت تهیه می شود . امروزه برای افزایش مقاومت سایش و جلوگیری از نفوذ مذاب درون قالب ، از دانه هایی با اندازه کوچکتر استفاده می شود. مقدار سیلیس در ماسه بیش از 90%است که مابقی آن را چسب های رسی (ایلیت ،کائو لینیت،بنتونیت و مونت مورلینیت) با حداقل 2% رطوبت تشکیل می دهد . برای مرطوب تر کردن خواص ماسه یا ایجاد ماسه ای ویژه از موادی بعنوان افزودنی تا حدود 2% به ماسه افزوده می شود.
ماسه های ماهیچه :
ماسه
ماهیچه ها عموما ازنوع سیلیسی هستند ولی در مواقعی از ماسه های زیرکنی ،
اولیونی ،کربنی و شاموتی نیز استفاده بعمل می آید . ازویژگی های بارز ماسه
های مصرفی برای ساخت ماهیچه ، شکل و اندازه ی ذرات آنها است ، بدینگونه که
استفاده از ذرات درشت و کروی شکل برای ساخت ماهیچه ،بدلیل داشتن قابلیت
نفوذ گاز بیشتر ، ترجیح داده می شود . معمولا ماسه ای که دارای بیش از 5 %
خاک (ذراتریز) باشد ، بدلیل کاهش یافتن قا بلیت از هم پاشیدگی آن ، برای
ساخت ماهیچه مناسب نیست ، علاوه بر این، خواص دیگری از قبیل دیر گدازی ،
پایداری ابعادی و شیمیایی ، قابلیت انتقال حرارت نیز از اهمیت زیادی
برخودار هستند . نکات مهم در ماسه های ماهیچه ای بشرح زیراست : وجود خاک رس
باعث تقلیل در کیفیت ماسه ماهیچه و نیز باعث اختلال در واکنش سایر چسب ها
با هم می گردد و بنا براین باید مقدار آن تا حد امکان در ماسه های ماهیچه
پائین باشد. امروزه نیز به دلیل دیر گدازی ، بالا بودن دانسیته حجمی و
ظرفیت حرارتی بیشتر ماسه های زیر کنی و اولیونی از دلائل اصلی کاربرد آنها
به جای ماسه سیلیسی به شمار می روند . در هر حال ، علی رغم وجود محدودیت
های از قیبل واکنش پذیری سیلیس با مذاب آهنی از این ماده به طور وسیعی به
عنوان ماده اصلی در ساخت ماهیچه ها استفاده می گردد
انواع ماسه از نظر شکل ظاهری :
ماسه های گرد
در
این حالت شکل ذرات ماسه در زیر میکروسکوپ ، کروی است. اکثر ماسه های
مصنوعی از نوع ماسه های گرد هستند که کیفیت سطحی بهتری را ایجاد می کند و
قابلیت عبور گاز بهتری نیز دارد ( قابلیت عبور گاز به تخلخل ماسه مربوط است
).
ماسه های شبهه گرد
این نوع ماسه در قسمت هایی گرد و در قسمت هایی گوشه دار است.
ماسه های گوشه دار
این
ماسه کاملاً گوشه دار است و بطور کامل در هم چفت می شوند و استحکام
بالاتری ارائه می دهد و از نظر حمل و نقل قالب و حرکت مذاب و فشار مذاب ،
استحکام بالاتری دارد اما قابلیت عبور گاز کم است.
ماسه های مخلوط
این ماسه ها شکل خاصی ندارند.
انواع ماسه از نظر ترکیب شیمیایی :
ماسه سیلیسی ( SiO2 )
سیلیس
یک حالت آلوتروپیک و چند ساختاره دارد و در دماهای مختلف ، ساختارهای
متفاوتی دارد ( منگنز، کبالت ، قلع و زیرکنیوم نیز آلوتروپیکند ). در نتیجه
اگر با سرعت های مختلف سرد شود ، خواص متفاوتی ارائه می کند ( در طراحی
قالب برای مواد دیر گداز ، مشکل ساز است زیرا منجر به ترک خوردن بدنه قالب
می شود ).
همان
طور که از وزن مخصوص ها ( دانسیته ها ) ملاحظه می شود ، با تغییرات دما ،
انبساط و انقباض در ابعادشان بوجود می آید که باعث شکست قالب می شود (
بیشترین تغییرات را کریستوبالیت دارد ).
یک مزیت ماسه سیلیسی ، وجود معادن زیاد و ارزانی آن است.
متوسط
ضریب انبساط این ماسه Cm/Cm ºC6-10×16.2 است ( یک نمونه استاندارد از ماسه
می سازیم و تا دمای مورد نظر می بریم و نگه می داریم سپس یک درجه اضافه می
کنیم و طول را اندازه گیری می کنیم ).
این
ماسه برای ریخته گری قطعات آهنی و فولادی و فولاد آلیاژی مناسب نیست و
بصورت ماسه Backing استفاده می شود. در چدن ریزی معمولاً از ماسه سیلیسی
مصنوعی استفاده می شود.
ماسه زیرکنیوم ( ZrO2.SiO2 )
زیر در طبیعت همراه با سیلیس است. غلظت زیر در ماسه بین 40 تا 50 درصد است.
این
نوع ماسه خاصیت انبساط حرارتی دارد و ضریب انبساط حرارتی آن حدوداً Cm/Cm
ºC6-10×4.5 است که از ماسه سیلیسی پایین تر است و برای مواد قالب و آجر و
بدنه کوره مناسب است.هدایت حرارتی این ماسه بالاتر است و سریع تر خنک می
شود ( 4 برابر کوارتز ). دارای وزن مخصوص ( دانسیته ) gr/Cm34.75 است که
تقریباً 2 برابر ماسه سیلیسی است که یک مزیت است زیرا در واقع چگالی توده ،
زیاد است و یک بخش از نیروی مذاب را خنثی می کند.
تحمل
دمایی ماسه زیرکونی بالاست و خاصیت دیرگدازی خوبی دارد درنتیجه برای فلزات
با دمای ذوب بالا کاربرد دارد( حدوداً درºC 2000 به حالت خمیری در می آید
). از دیگر خصوصیات این ماسه دانه های گرد و منظم و عدم خیس
شدن
توسط مذاب ( نمی چسبد ) و عدم تمایل به واکنش شیمیایی با اکثر فلزات است و
اگر سرباره یا مذاب ، دارای موادی باشند که باعث خوردگی بدنه کوره شود ،
این ماسه مقاوم است.
ماسه الوینی سیلیکات های مضاعف آهن و منیزیم (Mg.Fe)2SiO2 )
Forsterite 2MgO.SiO2 , Fayalite 2FeO.SiO2
دیرگدازی
این ماسه نسبت به ماسه سیلیسی بالاتر و از ماسه زیرکونی کمتر است ( ºC
1850-1750 ) که برای فولاد ساده و پر کربن و کم آلیاژ مناسب است. این ماسه
دارای وزن مخصوص ( دانسیته ) gr/Cm3 3.3 است و از نوع ماسه های گوشه دار
است. انبساط حرارت این ماسه از ماسه سیلیسی کمتر و از ماسه زیرکونی بالاتر
است.
ماسه کرومیتی ( FeO.Cr2O3 )
این
ماسه عمتاً بصورت ماسه رویه ( Facing Sand ) استفاده می شود ، دیرگدازی
بالایی دارد ( ºC 1850-1450 ) که هر چه اکسید کرم کمتر باشد بهتر است. این
ماسه دارای وزن مخصوص ( دانسیته )gr/Cm34.5 می باشد. در شرایطی که با چسب
خاک رس ترکیب شود در ºC 1000دارای انبساط حرارتی mm/mm0.17 است ، سیلیس در
همان شرایط دارای انبساط حرارتی mm/mm 0.6و زیر mm/mm0.076است. این ماسه ،
سیاه رنگ و از نوع ماسه های گوشه دار است.
ماسه شاموتی Al2O3.SiO2
این
ماسه دارای دیرگدازی ºC 1750-1670است که هر چه Al2O3 بیشتر باشد ، بهتر
است. از این ماسه در ریخته گری بصورت آجر و بدنه کوره استفاده می شود. این
آجر نارنجی نیز دارای انبساط و انقباض بوده و ترک می خورد. این ماسه برای
فولاد آلیاژی و کم کربن مناسب است.
انتخاب ماسه :
از
چند نقطه باید نمونه گیری کرد و تست ترکیب شیمیایی و دیر گدازی و ....
انجام داد ( برای اینکه رطوبت و مواد همراه ماسه تبخیر نشود ، باید در ظرف
بسته نمونه برداری کرد.
خواص عمومی ماسه ریختگی :
1)استحکام در حالت تر ( Green Strength ) : استحکام فشاری و برشی در گوشه ها
2)استحکام در حالت خشک ( Dry Strength )
3)استحکام
در حالت حرارتی ( Hot Strength ) : سریع به دمای بالا می رسد ، وقتی رطوبت
خود را از دست می دهد نباید شکل خود را از ذست بدهد زیرا باعث ایجاد ترک و
خرد شدن یا پلیسه و زائده و رگه می شود.
4)قابلیت
عبور گاز ( Permeability ) : گاز متصاعد شده از چسب و پوشش و هوای داخل
باید خارج شود. به شکل و دانه مواد قالب و میزان کوبش و چسب و رطوبن بستگی
دارد.
5)پایداری حرارتی ( Thermal Stability ) : ابعاد خود را حفظ کند و ضریب انبساط حرارت پایین داشته باشد.
6)دیرگدازی ( Refractoriness ) : مواد قالب تغییر حالت ندهد و سوخته و ذوب نشود و مقاوم به حرارت باشد.
7)قابلیت شکل گیری ( Flowability ) : به اندازه دانه بستگی دارد.
8)کیفیت سطحی ( Produces Good Casting Finish ) : به خواص فیزیکی دانه بستگی دارد.
9)قابلیت فروپاشی ( Collapsibility ) : تابع نوع چسب مصرفی است.
10)قابلیت بازیافت ( Reusable )
11)تهیه و کنترل ساده
12)درت خنک کنندگی ( Remove Heat )
ماسه
سیلیسی را با خاک اره مخلوط کرده و جلو انبساط و انقباض را می گیرند یا با
چسب سیلیکات سدیم و مواد افزودنی برای راحت جدا شدن مخلوط می کنند.
رطوبت
در صنعت بین 4 تا 6 درصد وزنی است ، اگر رطوبت کم باشد ، استحکام تر کاهش
می یابد و اگر زیاد باشد ، باعث ایجاد موک گازی می شود
بررسی ماسه های قالبگیری و ماسه ماهیچه در فرآیند ریخته گری قالب موقت
ماسه ی قالبگیری:
سیلیس
(sio2 )، مهمترین جزء ماسه های مصرفی در قالبگیری می باشد، این ماده دارای
دیر گدازی بالامیباشد و می توان از ماسه های طبیعی که معمولا دارای اندازه
ای یکنواخت و کروی هستند این ماده را بدست آورد و یا با عمل شکست در ماسه
سنگ های بزرگ ، ماسه ای با ذرات زاویه دار و اندازه غیر متناسب تهیه نمود.
در ماسه ها ی قالبگیری خواص فیزیکی بسیار مهم است . معمولا ماسه ها بصورت
کروی و دانه بندی یکنواخت تهیه می شود . امروزه برای افزایش مقاومت سایش و
جلوگیری از نفوذ مذاب درون قالب ، از دانه هایی با اندازه کوچکتر استفاده
می شود. مقدار سیلیس در ماسه بیش از 90%است که مابقی آن را چسب های رسی
(ایلیت ،کائو لینیت،بنتونیت و مونت مورلینیت) با حداقل 2% رطوبت تشکیل می
دهد . برای مرطوب تر کردن خواص ماسه یا ایجاد ماسه ای ویژه از موادی بعنوان
افزودنی تا حدود 2% به ماسه افزوده می شود.
ماسه های ماهیچه :
ماسه
ماهیچه ها عموما ازنوع سیلیسی هستند ولی در مواقعی از ماسه های زیرکنی ،
اولیونی ،کربنی و شاموتی نیز استفاده بعمل می آید . ازویژگی های بارز ماسه
های مصرفی برای ساخت ماهیچه ، شکل و اندازه ی ذرات آنها است ، بدینگونه که
استفاده از ذرات درشت و کروی شکل برای ساخت ماهیچه ،بدلیل داشتن قابلیت
نفوذ گاز بیشتر ، ترجیح داده می شود . معمولا ماسه ای که دارای بیش از 5 %
خاک (ذراتریز) باشد ، بدلیل کاهش یافتن قا بلیت از هم پاشیدگی آن ، برای
ساخت ماهیچه مناسب نیست ، علاوه بر این، خواص دیگری از قبیل دیر گدازی ،
پایداری ابعادی و شیمیایی ، قابلیت انتقال حرارت نیز از اهمیت زیادی
برخودار هستند . نکات مهم در ماسه های ماهیچه ای بشرح زیراست : وجود خاک رس
باعث تقلیل در کیفیت ماسه ماهیچه و نیز باعث اختلال در واکنش سایر چسب ها
با هم می گردد و بنا براین باید مقدار آن تا حد امکان در ماسه های ماهیچه
پائین باشد. امروزه نیز به دلیل دیر گدازی ، بالا بودن دانسیته حجمی و
ظرفیت حرارتی بیشتر ماسه های زیر کنی و اولیونی از دلائل اصلی کاربرد آنها
به جای ماسه سیلیسی به شمار می روند . در هر حال ، علی رغم وجود محدودیت
های از قیبل واکنش پذیری سیلیس با مذاب آهنی از این ماده به طور وسیعی به
عنوان ماده اصلی در ساخت ماهیچه ها استفاده می گردد
مخلوط ماسه ماهیچه برای قطعات ریخته گری فولادی :
برای
قطعاتی با ضخامت 9.5-11 تا 12 میلیمتر و ماهیچه های کوچک می توان
روغن(oil)،صمغ (Resin)،نشاسته(Cereal)و چسب های مخلوط شده بکار برد .قطعات
ضخیم تر با اندازه 16 تا25 میلیمتر که ماهیچه های بزرگ دارند به استحکام
بیشتری نیاز داشته و برای ماهیچه های آن میتوان از چسب های زیر استفاده
کرد:
صمغ یا روغن همراه با نشاسته ؛ خاک رس(clay) یا بنتونیت (bentonite) قیر (pitch) و چسب های مخلوط با قیر نیز به کار گرفته می شوند.
برای
ماهیچه های خارجی در قطعات با ضخامت زیاد ،خاک رس و چسب بنتونیت می تواند
به کار رود.مخلوطی با 50% خاک رس و50%بنتونیت نتیجه بهتری را ببار می آورد.
برای ماهیچه های داخلی در قطعات با ضخامت زیاد،نشاسته و چسب های روغنی می تواند به کار رود.
در
برخی از موارد که ضخامت خیلی زیاد است،چسب خاک رس - بنتونیت را می توان
برای سطح ماهیچه مورد استفاده قرار داد. در همه موارد فوق الذکر یک ماسه
پشتی نرم در پشت ماسه رویی به کار گرفته می شود .
ماسه قالبگیری
تعریف:
همانگونه
که قبلاً گفته شد ماسه عبارتست از ذراتی که از سنگها و صخره ها بدست می
آید و قطر آنها بین 2/0 تا 2 میلیمتر است و ذرات کوچکتر از آن خاک نام
دارد. این ذرات به همراه مواد دیگری قابلیت شکل گیری پیدا می کند که به آن
ماسه قالبگیری یا ماسه ریخته گری می گویند. مخلوط ماسه ریخته گری تر همیشه
شامل دانه های ماسه، چسب و رطوبت است. این مواد اجزاء اصلی ماسه قالبگیری
هستند و مواد دیگری ممکن است جهت مشخصات لازم به آنها اضافه شود.
مشخصات ماسه قالبگیری:
با
توجه به مطالبی که در فصل اول پیرامون پیدایش ماسه گفته شد مشخص می گردد
که آنچه بنام ماسه خوانده می شود می تواند مختلف باشد و این وظیفه ریخته
گران است که مناسبترین نوع آنرا انتخاب کنند و مسلماً ماسه ریخته گری
بایستی دارای مشخصاتی باشد تا قطعه بدون عیت تهیه گردد. مهمترین این مشخصات
عبارتند از:
الف: قابلیت فرم گیری
برای
اینکه تمام قسمتهای مدل توسط ماسه فرم پر شود بایستی تمام دانه های ماسه
بتوانند به یکدیگر بچسبند. ضمناً دانه ها بایستی در مقابل حرکت مذاب مقاومت
کرده و شسته نشوند.
قابلیت
چسبندگی در بعضی از ماسه ها بطور طبیعی می باشد مثل ماسه محتوی خاک رس و
در بعضی دیگر این خاصیت وجود نداشته و باید مصنوعاً چسب به آنها اضافه
نمود. روی خاصیت فرم گیری و چسبندگی ماسه وضعیت سطح خارجی و شکل ماسه ها
نیز اثر دارد.
ب: ثبات حرارتی
حرارت
ناشی از مذاب و قطعه ریخته شده باعث انبساط سطوح ماسه می شود که ممکن است
سطح قالب ترک بردارد یا کیس دار و چروکیده شود مگر اینکه ماسه قالبگیری
نسبتاً در تحت حرارت سریع ابعادش ثابت بماند.
ج: دیرگدازی
ماسه
بایستی از نظر حرارتی مقاوم بوده و نرم و شیشه ای نشود چون در این صورت به
جداره قطعه ریخته شده چسبیده و سطوح آن را معیوب می کند و تمیز کردن آنها
را مشکل می سازد. البته این شیب بیشتر در ریخته گری فلزات و آلیاژهای با
نقطه ذوب بالا مانند آلیاژهای آهنی دیده می شود.
درجه حرارت شیشه ای شدن یا زینتر عبارت است از درجه حرارتی که ذرات ماسه شروع به چسبیدن به یکدیگر می نمایند.
د: استحکام تر
ماسه ریخته گری باید پس از فرم گیری بتواند شکل خود را حفظ نماید و استحکام کافی جهت جابجا شدن را داشته باشد.
ه: استحکام خشک
ماسه
قالبگیری بایستی پس از تمام شدن رطوبت سطح قالب در اثر تماس با فلز مذاب
در برابر فشار مذاب استقامت کرده و سطوح آن خراب نشود و ذرات ماسه از
یکدیگر جدا نشوند.
و: قابلیت عبور گاز
ماسه
متراکم شده باید به مقدار معینی خاصیت عبور گاز داشته باشد زیرا نه تنها
فلز مذاب هنگام انجماد مقداری گاز از خود متصاعد می کند بلکه مقدار هوائی
که داخل محفظه قالب حبس شده هنگام ریختن فلز مذاب حجمش چندین برابر می شود.
رطوبت ماسه در اثر حرارت ایجاد شده تولید بخار آب می کند، در ماسه ممکن
است مقداری گرافیت و ذغالسنگ وجود داشته باشد که در اثر حرارت تولید گاز می
نماید. تمام این گازها و بخارها بایستی از طریق ماسه بخارج هدایت شوند.
بدین جهت قابلیت عبور گاز بسیار قابل توجیه است. قابلیت عبور گاز تابعی از
مقدار چسب، میزان رطوبت، بزرگی دانه ها، میزان تراکم، شکل ظاهری و درجه
یکنواختی ماسه است که بعداً در این مورد توضیح داده خواهد شد.
ز: قابلیت ایجاد سطوح تمیز
ح: قابلیت استعمال مجدد
ط: تهیه و کنترل آن آسان باشد.