Bake hardening steels
Description
The composition and processing of these steels are designed to promote a significant increase in yield strength during low-temperature heat treatment, particularly paint curing.
ArcelorMittal Bake hardening steels can thus achieve higher strength in the finished part while retaining good forming performance. The gain in yield strength through the "bake hardening" (BH) effect is generally greater than 40 MPa. Thanks to this BH effect, ArcelorMittal steels offer two advantages compared to conventional drawing quality steels:
- Improved dent resistance in all finished parts in the case of low forming strains (hood, roof, doors and wings);
- Substantial weight reduction potential at equivalent dent resistance (the decrease in thickness is offset by increased yield strength resulting from the heat treatment process).
Bake hardening steels thus offer a suitable response to automotive bodywork requirements. By providing an excellent drawability-dent resistance combination, they enhance vehicle weight reduction and aesthetics.
Applications
Steels in the BH range are designed for visible (door, hood, tailgate, front wing, roof) and structural (underbody, reinforcement, cross member, lining) parts.
Designation and standard
|
EN 10268 :2006 |
EN 10268 :2006 + EN 10152 :2009 |
EN 10346 :2009 |
|
HC180B |
HC180B+ZE |
HX180BD+Z |
|
|||
|
HC220B |
HC220B+ZE |
HX220BD+Z |
|
HC260B |
HC260B+ZE |
HX260BD+Z |
|
HC300B |
HC300B+ZE |
HX300BD+Z |
|
|||
|
While the ArcelorMittal grades conform perfectly well to the indicated EN standards, ArcelorMittal grades generally offer tighter mechanical properties (see table below).
The 195 BH grade corresponds to Japanese standards.
Guaranteed for ISO 20X80 test specimen in the transverse direction
|
YS (MPa) |
UTS (MPa) |
ef (%) |
r |
n |
BH2 (MPa) |
|||
|
180 - 230 |
300 - 360 |
≥ 34 |
≥ 1,6 |
≥ 0,17 |
≥ 35 |
|||
|
195 - 270 |
340 - 400 |
≥ 32 |
≥ 1,3 |
≥ 0,16 |
≥ 35 |
|||
|
220 - 270 |
340 - 400 |
≥ 32 |
≥ 1,5 |
≥ 0,16 |
≥ 35 |
|||
|
260 - 300 |
370 - 430 |
≥ 30 |
≥ 0,15 |
≥ 35 |
||||
|
300 - 360 |
420 - 480 |
≥ 28 |
≥ 0,14 |
≥ 40 |
||||
|
|||||||||
|
Chemical composition (%)
|
C |
Mn |
Si |
|
Max |
Max |
Max |
|
0,04 |
0,70 |
0,50 |
|
0,06 |
0,70 |
0,50 |
|
0,06 |
0,70 |
0,50 |
|
0,08 |
0,70 |
0,50 |
|
0,10 |
0,70 |
0,50 |
|
|||
|
Definition of BH2
"Bake hardening" is a controlled aging phenomenon related to the presence of carbon and/or nitrogen in solid solution in the steel. The BH2 parameter is used to evaluate the resulting increase in dent resistance. It is given by: BH2 = LYS - 2% PS, in which LYS is the lower yield stress measured after heat treatment and PS is the yield stress after initial 2% plastic pre-strain. BH2 measurement is a reliable and reproducible way to quantify the metal's ability to harden during cataphoresis.
The diagram below illustrates the Bake hardening mechanism and shows the displacement of carbon atoms in solution during heat treatment-typically 20 minutes at 170°C to block the dislocations generated by forming. This ultimately increases the metal's yield strength.
Available coatings and surface conditions
|
Uncoated |
Electrogalvanized |
Galvannealed |
Extragal® |
Ultragal® |
|
XX |
XX |
XX |
XX |
|
|
XX |
||||
|
XX |
XX |
XX |
XX |
|
|
XX |
XX |
XX |
XX |
|
|
X |
X |
X |
||
|
|||||
|
X Available - XX Available in visible part quality
For additional information about the availability of thin organic coatings for the ArcelorMittal range of BH steels, please refer to the coating technical sheets. Curing of these organic coatings may lead to changes in mechanical properties.
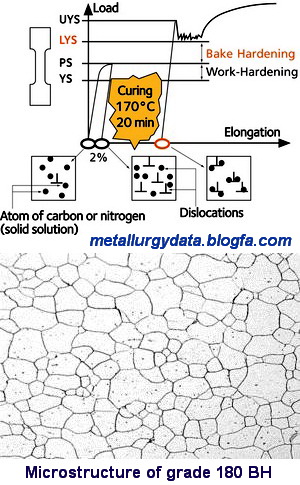