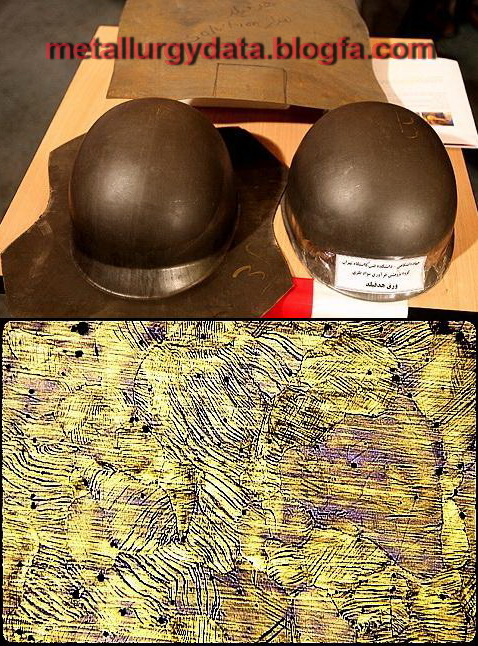
فولادهای هادفیلد
فولادهای
آستنیتی منگنز (حاوی حدود 1.2 درصد کربن و 12 درصد منگنز) در سال 1882
توسط رابرت هادفیلد (Robera Hadfoeld) ابداع و معرفی شدند. این خانواده از
فولادها به افتخار ایشان به نام هادفیلد معروف شدند. فولادهای آستنیتی
منگنزدار با داشتن ترکیب مناسب از چقرمگی، انعطاف پذیری، قابلیت کار سختی و
مقاومت در مقابل سایش، در نوع خود منحصر به فرد هستند. و دارای کاربرد
وسیع میباشند. این خانواده دارای کاربرد وسیع میباشند. این خانواده در
کنار ویژگیهای عالی، محدودیتهایی نیز دارند که عمده ترین آنها عبارتند
از:
- قابلیت ماشینکاری ضعیف
- استحکام تسلیم پائین (در محدوده MPA 415-345)
در
نتیجه برای قطعاتی که لازم است دقت ابعادی بالایی داشته باشند، یا در
تنشهای بالا در مقابل تغییر شکل مقاوم باشد، مناسب نیستند. انجام عملیاتی
نظیر چکش کاری، کوبش، پرس کاری، نورد سرد و شوک های انفجار بر روی سطح این
فولادها باعث افزایش استحکام تسلیم و بالا رفتن سختی سطح آنها (ضمن حفظ
انعطاف پذیری در مغز) می شود.
خواص فیزیکی فولادهای آستنیتی منگنزی
فولادهای
آستنیتی منگنزی با هدایت حرارتی کم و ضریب انبساط حرارتی زیاد، از
فولادهای ساده کربنی متمایز می شوند؛ این فولادها در درجه حرارت اتاق غیر
مغناطیسی هستند.
ترکیب شیمیایی فولادهای آستنیتی منگنزی و استانداردهای مرتبط
از
هنگام ابداع فولادهای هدفیلد، تغییرات گوناگون در هنگام ترکیب شیمیای آن
صورت گرفته است. برخی از این ترکیبها به عنوان ابداع مورد ثبت قرار
نگرفتهاند، تنها ترکیبهای محدود مورد استقبال واقع شدند و تکامل یافتند.
تغییرات عمده عموماً در میزان کربن و منگنز به همراه افزودن عناصر آلیاژی
نظیر نیکل، مولیبدن، وانادیم، تیتانیم و بیسموت، یا بدون افزودن عناصر
آلیاژبوده است. معروفترین و مهمترین طبقه بندی شیمیایی فولادهای هادفیلد،
به وسیله ASTM صورت گرفته است. این طبقه بندی تحت استاندارد ASTM AL28
ارایه شده است.
معیار استانداردهامعتبر عبارتند از:
JIS G5131 کربن
BS- 3100 BW 10 افزایش استحکام تسلیم
UNI 3160-83-GX 120 MnCr 1202
تاثیر ترکیب شیمیایی و عناصر مختلف بر خواص فولاد هادفیلد
عنصر کربن
عنصر
کربن بر همه ویژگیهای فولاد هادفیلد تاثیر معین و مشخص دارد. این تاثیرات
عبارتند از: افزایش درجه حرات Acm با افزایش میزان کربن، افزایش استحکام
تسلیم، افزایش استحکام کششی تا محدوده معین از کربن و سپس کاهش آن با
افزایش کربن، کاهش ازدیاد طول نسبی.
عنصر منگنز
منگنز تاثیر
اندکی بر استحکام تسلیم دارد. منگنز تا 14 درصد استحکام کششی و ازدیاد طول
نسبی را افزایش و در بالاتر از آن کاهش میدهد. منگنز عامل پایدار کننده
آستنیت است اما نمیتواند استحاله آستنیت را متوقف کند.
عنصر سیلیسیم
عنصر
سیلیسیم به ندرت به عنوان عنصر آلیاژی به ترکیب فولادهای هادفیلد اضافه می
شود، حضور آن عمدتاً به دلیل استفاده از این عنصر به عنوان اکسیژن زدا در
فرایند تهیه ذوب است. عنصر سیلسیم تا حدود 2 درصد استحکام تسلیم فولاد
هادفیلد را به مقدار کم افزایش می دهد. در بالاتر از 2.2 درصد کاهش سریع در
استحکام و انعطاف پذیرحاصل میشود. فولادهای هادفیلد حاوی بیش از 2.3 درصد
سیلیسیم قابلیت کار پذیر ندارند.
عنصر فسفر
میزان فسفر مجاز،
مطابق استاندارد 0.07 Al 28، ASTM درصد است، ولی از سال 1960 که دستیابی به
فرو منگنزهای حاوی مقادیر کم فسفر امکان پذیر شد، تولید کنندگان فولاد
هادفیلد به کاهش فسفر و نگهدارآن در حد کمتر از 0.04 درصد اقدام کردند.
اثرات فسفر عبارتند از: کاهش انعطاف پذیری به خصوص در پایینتر از درجه
حرارت اتاق. در بالاتر از 0.06 درصد ضمن کاهش انعطاف پذیری، تمایل به پارگی
گرم در درجه حرارتهای بالا را افزایش می دهد. کاهش عنصر فسفر در حداقل
ممکن، همواره و بخصوص در موارد که قطعات جوشکاری میشوند توصیه میگردد.
میزان فسفر در الکترودهای جوشکای در فولادهای منگنزی، باید در پائینترین
حد باشد.
اگر مقادیر منگنز و کربن هر دو با هم کم باشد برای
مثال% 53/0کربن و% 3/ 8 منگنز یا 62/0 کربن و% 1/8 منگنز ، میزان کار
سختی افزایش مییابد اما این امر سبب افزایش مقاومت سایشی نخواهد شد.
تیتانیوم
در این فولادها با تشکیل کاربیدهای پایـــدار مقدار کربن در آستنیت را
کاهش میدهد ودر نتیجه خواص بدست آمده می تواند مشابه حالت کاهش کربن در
فولاد باشد. همچنین تیتانیوم می تواند تا حدی اثر فسفر را خنثی نماید .
همچنین دیده شده است که افزایش مقادیر خیلی کم ( کمتر از% 1 /0 ) تیتانیوم
، وانادیم ، بور ، زیرکونیم و نیتروژن منجر به ریزتر شدن دانهها در این
فولادها می شود . اما مقادیر بیشتر این عناصر ممکن است کاهش چشمگیر قابلیت
چکش خوارى را به همراه داشته باشند. مقادیر بیشتراز % 2/0 نیتروژن میتواند
باعث ایجاد تخلخلهای گازی در قطعات ریختهگی شود .
گوگرد به ندرت
بر خواص فولادهای هادفیلد اثر میگذارد. زیرا به دلیل حضور منگنز وجود
گوگرد منجر به تشکیل سولفات منگنز به جای سولفات آهن میشود.به همین دلیل
در استاندارد 128A مقدار عنصر گوگرد ذکر نشده است.اما در هر حال بهتر است
مقادیر گوگرد تا حد امکان در ترکیب کم باشد زیرا این ترکیبات ممکن است با
ایجاد مکانهای بالقوه ای شرایط مناسب برای جوانه زنی شکافهای خستگی در
قطعات را بوجود آورند و البته این امری ناخوشایند است.
فولادهای
آستنیتی با مقادیر زیاد منگنز (مقادیر منگنز بیش از % 15 ) اخیراً برای
استفاده در موقیتهایی که نیازمند قابلیت نفوذ مغناطیسی کم و استحکام وسختی
در دمای پاییناند، توسعه یافتهاند. البته این کاربردها از توسعه
تکنولوژی سوپرهادیها ، تحقیقات ذوب هسته ای و احساس نیاز به مواد ساختاری
( برای ذخیره و انتقال گازهای مایع ) سرچشمه میگیرند.
برای کاهش
قابلیت نفوذ مغناطیسی ، این آلیاژها حاوی مقادیر کمتر کربن نسبت به مقدار
معمول فولادهای هادفیلد هستند . البته کاهش تنش تسلیم با اضافه کردن
عناصری مثل تیتانیوم ، وانادیم ، نیتروژن ، کرم و مولیبدن جبران خواهد شد .
همچنین کرم باعث ایجاد مقاومت خوردگی خواهد شد( این خصوصیت در بعضی از
سیستمهای برودتی مورد نیاز است) .
یکی از نکات قابل توجه درمورد
این فولادها این است که ریختهگری این دسته از فولادها خیلی راحت نیست
چرا که مذاب این فولادها با نسوزهای سیلیکاتی کوره واکنش داده و باعث
تخریب نسوز کوره می شود و برای حل این مشکل باید به جای نسوزهای سیلیکاتی
از اکسید آلومینیوم استفاده کنیم.
همانطور که میدانیم یکی از
کاربردهای وسیع این فولادها در خرد کنندههای مواد معدنی مثل سنگ شکنهای
فکی و ژیراتوری است . نکته جالب در این میان این است که این فولادها در
اثر ضربه از مقاومت سایشی بسیار بالایی برخوردار میشوند که علت آن این است
که در اثر ضربه دانههای موجود در سطح به شدت ریز شده و به نانو دانه
تبدیل میشوند و در حقیقت میتوان گفت به ساختاری شبه آمورف دست مییابیم
که منجر به بهبود خواص از جمله مقاومت سایشی خواهد شد.